Understanding Plastic Molding for Electrical Applications
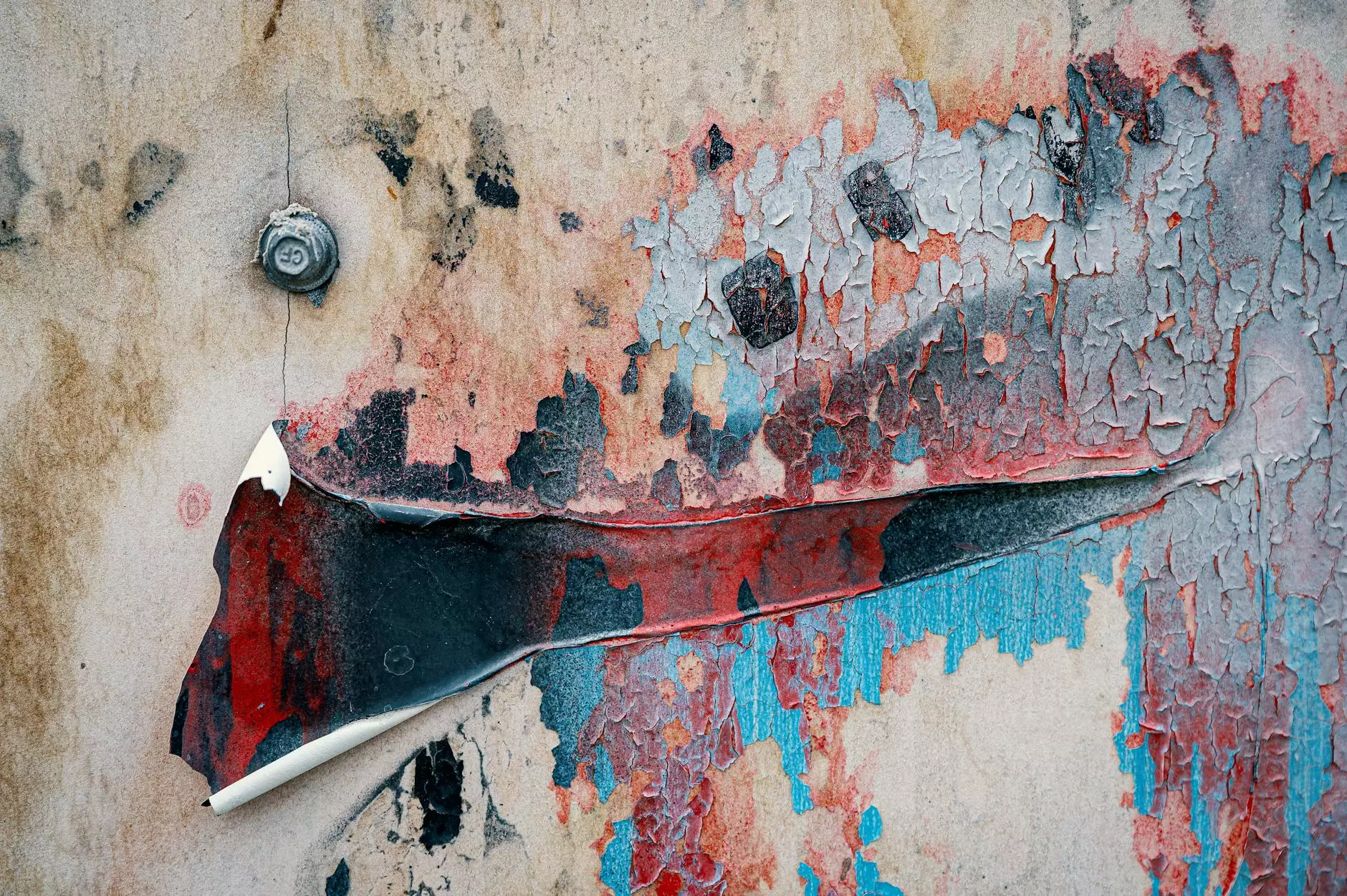
Plastic molding for electrical applications is a critical process that enables the manufacturing of high-quality electrical components. With the growing demand for reliable and efficient electrical products, the significance of advanced molding techniques cannot be overstated. This article will delve into the nuances of plastic molding, its benefits, applications, and the role it plays in enhancing electrical manufacturing.
What is Plastic Molding?
Plastic molding is a manufacturing process that involves shaping plastic materials into desired forms. The process typically involves heating plastic until it becomes malleable, then placing it into a mold. Once cooled, the plastic hardens and retains the shape of the mold. This method is widely used across various industries, but it holds particular importance in the electrical sector.
The Importance of Plastic Molding for Electrical Components
Plastic materials have become increasingly prevalent in electrical components due to their lightweight properties, resistance to corrosion, and insulating capabilities. Here are some reasons why plastic molding for electrical parts is crucial:
- Cost-Effectiveness: Plastic molding reduces the overall manufacturing costs compared to traditional materials like metal. This makes it possible for manufacturers to produce high-quality components at lower prices.
- Design Flexibility: Plastic molding allows for intricate designs that can accommodate various functionalities within electrical components, leading to innovative product development.
- Durability: Molded plastic parts can withstand harsh environmental conditions, making them ideal for outdoor and industrial applications.
- Insulating Properties: Plastic is an excellent electrical insulator, preventing short circuits and enhancing safety in electrical products.
Types of Plastic Molding Techniques
There are several techniques employed in plastic molding, each offering unique advantages for electrical component manufacturing. The most common methods include:
1. Injection Molding
Injection molding is one of the most widely used plastic molding processes. It involves injecting molten plastic into a mold under high pressure, allowing for the creation of complex shapes. This technique is highly efficient for producing large quantities of identical parts, making it ideal for mass manufacturing electrical components.
2. Blow Molding
Blow molding is primarily used to create hollow plastic parts. In this process, air is blown into a heated plastic tube, causing it to expand and take the shape of the mold. This technique is useful for producing items such as electrical enclosures and housings.
3. Rotational Molding
Rotational molding involves placing plastic powder into a mold that is heated while being rotated on two axes. This approach allows for the uniform coating of the mold's interior, resulting in thicker and more durable parts. It is often used for larger electrical components that require strength and resilience.
4. Thermoforming
Thermoforming is the process of heating a plastic sheet until soft and then stretching it over a mold. This method is suitable for producing thinner, larger pieces where precision is of less precedence. It is often used for packaging materials and covers for electrical devices.
Benefits of Using Plastic Molding for Electrical Components
The adoption of plastic molding technologies in the electrical industry provides a multitude of benefits:
- Enhanced Electrical Insulation: The electrical insulation properties of plastic significantly contribute to the safety and efficiency of electrical devices.
- Improved Aesthetics: Plastic components can be molded into aesthetically pleasing designs, allowing for varied colors and textures that appeal to consumers.
- Reduced Weight: Using plastic over metal contributes to lighter electrical products, improving portability and ease of use.
- Shorter Production Times: Modern plastic molding techniques allow for faster turnaround times, helping manufacturers meet market demands.
Applications of Plastic Molding in Electrical Manufacturing
The applications of plastic molding within the electrical industry are vast. Here are some key examples:
1. Electrical Housings
Plastic housings are commonly used to protect electrical components from environmental factors. They provide a lightweight and durable enclosure that enhances the longevity and performance of devices.
2. Connectors and Switches
Plastic molded parts are often used for electrical connectors and switches due to their excellent insulating properties, which help prevent accidental shorts and enhance usability.
3. Circuit Breakers
This safety mechanism uses plastic casings to house sensitive electrical components. Plastic molding enables the creation of complex geometries necessary for effective protection mechanisms.
4. Cable Management Solutions
Molding is used to create clips, trays, and conduits that organize and secure electrical cables. These components not only maintain order but also enhance safety by minimizing wear and tear.
Choosing the Right Material for Plastic Molding
The choice of material is vital when it comes to plastic molding for electrical components. Common materials include:
- ABS (Acrylonitrile Butadiene Styrene): Known for its robustness and impact resistance, ABS is often used for parts that require high durability.
- Polycarbonate: This material is highly transparent and provides excellent electrical insulation. It is often used in applications where visibility of internal components is required.
- PVC (Polyvinyl Chloride): PVC offers good chemical resistance and is widely used in electrical insulation and conduit systems.
- Polypropylene: Known for its lightweight properties and resistance to moisture, polypropylene is often utilized in packaging and lightweight electrical components.
Conclusion: The Future of Plastic Molding in Electrical Manufacturing
As technology advances, the landscape of plastic molding continues to evolve. With improvements in materials, molding techniques, and design software, the efficiency and capabilities of plastic molding for electrical components are set to expand further. Manufacturers like DeepMould.net are at the forefront of these advancements, leading the way in innovation and quality.
In summary, plastic molding plays a vital role in the electrical manufacturing industry, offering significant advantages such as cost-efficiency, design flexibility, and enhanced safety. As businesses embrace new technologies and methodologies, the future of plastic molding for electrical applications looks promising, ensuring that manufacturers can meet the ever-growing demands of the market while maintaining high standards of quality and performance.