The Ultimate Guide to Oil Seals: Choosing the Right Oil Seals Manufacturer
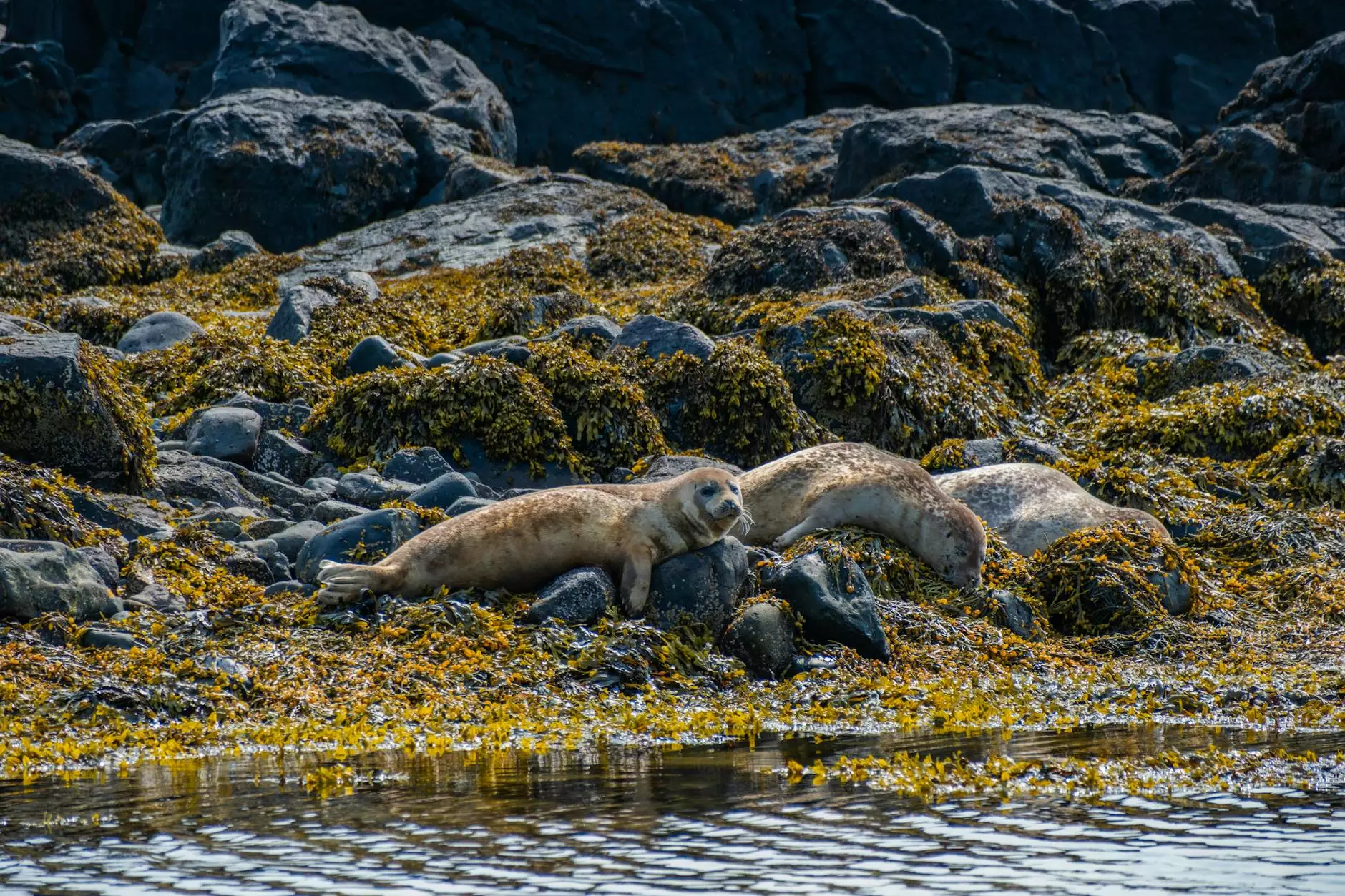
In the world of industrial and automotive machinery, the significance of oil seals cannot be underestimated. These small yet critical components play a major role in ensuring the efficient operation of various machines, especially in diesel engines. This article delves into the intricate details of oil seals, their purpose, application, and how to select the perfect oil seals manufacturer for your business needs.
Understanding Oil Seals
Oil seals, also known as radial shaft seals, are specially designed components that prevent the leakage of fluids, such as oil or grease, while simultaneously keeping dirt and other contaminants from entering the machinery. Oil seals are commonly made from elastomeric materials and come in various shapes and sizes, depending on their application.
Why Are Oil Seals Important?
Oil seals fulfill several vital functions in machinery:
- Prevent Fluid Leaks: They significantly reduce the risk of oil leaks, which can lead to severe machinery malfunction.
- Protect Internal Components: Oil seals keep contaminants out, thus safeguarding internal engine parts from dirt and debris.
- Enhance Operational Efficiency: Proper sealing can maintain optimum pressure and temperature within the machinery, enhancing overall performance.
- Extend Equipment Lifespan: Quality oil seals can extend the life of machinery by reducing wear and tear on critical components.
Types of Oil Seals
There is a diverse range of oil seals available in the market, which can be categorized based on their design and material. Here are some common types:
- Single-lip Seals: These are the most common type of oil seals, featuring a single sealing lip. They are effective in keeping oil contained and preventing contamination.
- Double-lip Seals: Designed with two sealing lips, these seals provide better protection against dust and moisture, making them ideal for more demanding applications.
- Spring-loaded Seals: Incorporating a spring mechanism, these seals maintain contact with the shaft, ensuring a tight seal even under varying operational conditions.
- Mechanical Seals: Often used in high-pressure applications, mechanical seals consist of both static and rotating faces, providing a more robust sealing solution.
Choosing the Right Oil Seals Manufacturer
Selecting an appropriate oil seals manufacturer is crucial for ensuring that your machinery operates efficiently and reliably. Here are some key factors to consider:
1. Industry Experience
Look for manufacturers that have a proven track record in producing oil seals. An experienced manufacturer will have a deep understanding of the various challenges and requirements specific to different applications.
2. Quality Assurance
Quality is paramount when it comes to oil seals. Verify that the manufacturer adheres to stringent quality control processes, such as ISO certifications, to ensure that every product meets high standards.
3. Material Options
Oil seals can be made from various materials like nitrile, fluorocarbon, or silicone rubber. Choose a manufacturer that offers a wide range of materials, allowing you to select the most suitable option for your needs.
4. Customization
Not all machinery is the same, and sometimes you may need customized oil seals for specific applications. Ensure that the manufacturer can produce tailor-made solutions to meet your unique requirements.
5. Technical Support
Another significant factor to consider is the level of technical support the manufacturer provides. They should be willing to assist with any questions or issues regarding installation and application of the oil seals.
6. Timely Delivery
A reliable manufacturer should be capable of meeting deadlines and delivering products in a timely manner to ensure that your operations are not hindered.
Common Applications of Oil Seals
Oil seals are used across a wide array of industries, including:
- Automotive: Essential for engines, transmissions, and differential applications.
- Industrial Machinery: Used in pumps, motors, and gearboxes to maintain fluid integrity.
- Aerospace: Critical for sealing hydraulic systems and engines.
- Marine: Protecting engines, gearboxes, and hydraulic systems from seawater and other contaminants.
- Construction Equipment: Used in heavy machinery to protect against dust and oil leaks in harsh environments.
Tips for Maintenance and Replacement of Oil Seals
Proper maintenance and timely replacement of oil seals are vital for optimal functionality. Here are some tips:
- Regular Inspections: Frequently inspect oil seals for signs of wear, such as cracking or deformation.
- Monitor Fluid Levels: Ensure that fluid levels are adequate to avoid excessive pressure on seals.
- Temperature Control: Avoid exposing oil seals to extreme temperatures that can lead to premature failure.
- Prompt Replacement: Replace any worn or damaged seals immediately to prevent costly leaks and equipment damage.
Conclusion
In conclusion, oil seals are essential components in the machinery of various industries, playing an integral role in functionality and reliability. By understanding their importance, types, and applications, along with how to select a reputable oil seals manufacturer, businesses can significantly improve operational efficiency and extend the lifespan of their machinery.
At Client Diesel, we pride ourselves on being a leading provider of diesel engine parts, including high-quality oil seals tailored to meet the diverse needs of our customers. Whether you are an automotive professional or an industrial contractor, we are here to provide you with the best solutions in spare parts to keep your machinery performing at its best.