The Low Pressure Casting Process: Transforming Business in Art Supplies and Design
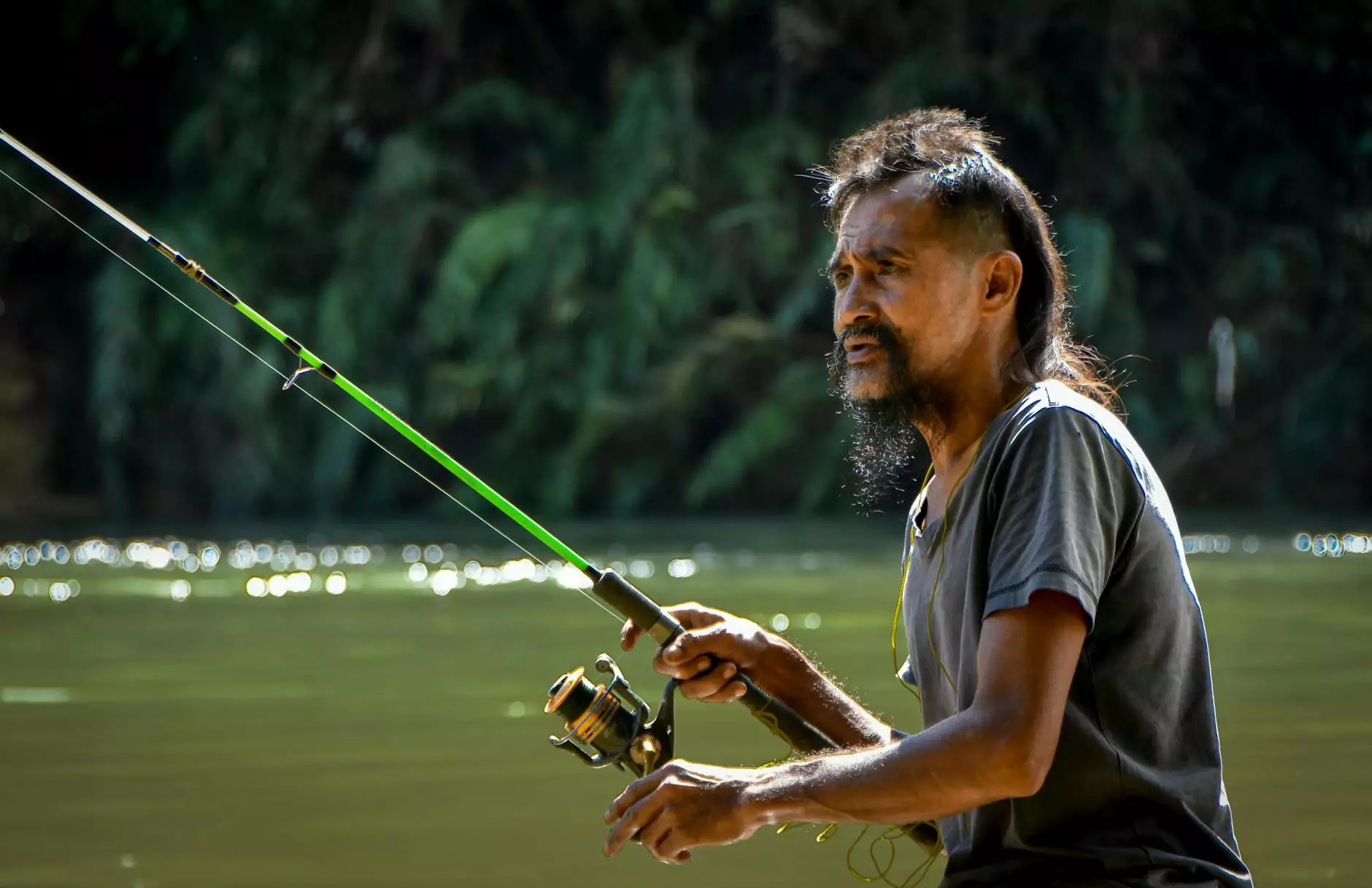
In today's competitive landscape, businesses must continually innovate to stay ahead. The low pressure casting process stands out as a transformative technique that has significantly impacted multiple industries, including art supplies, product design, and 3D printing. This article delves deep into the mechanics of the low pressure casting process and its implications for businesses, providing you with insights that could enhance your operations and product offerings.
What is the Low Pressure Casting Process?
The low pressure casting process is a manufacturing method designed primarily for producing intricate metal parts with exceptional quality and precision. Unlike conventional casting methods that rely on gravity, low pressure casting utilizes controlled air pressure to inject molten metal into a mold. This technique not only minimizes the presence of air pockets and flaws but also ensures a consistent flow of material.
Key Components of Low Pressure Casting
- Mold: Typically made from high-quality materials, molds are designed to withstand repeated use and high temperatures.
- Metal Alloy: The choice of metal alloy significantly affects the final product's properties, such as strength, weight, and corrosion resistance.
- Pressure System: This system regulates the application of low pressure to ensure that the molten metal is injected smoothly into the mold.
- Cooling Mechanism: An efficient cooling system is essential to control the solidification rate, ensuring the final product meets dimensional specifications.
Benefits of the Low Pressure Casting Process
The advantages of employing the low pressure casting process are numerous and compelling. Businesses engaged in art supplies and product design can reap the rewards of enhanced operational efficiencies and superior product quality. Here are some key benefits:
1. Superior Quality Parts
The low pressure casting process results in parts that exhibit a high level of detail and minimal defects. The controlled pressure prevents inclusions and porosity, leading to strong, durable products. This is crucial for businesses in the art supplies sector, where precision and quality are paramount for customer satisfaction.
2. Cost-Effectiveness
While initial setup costs may be higher, the long-term benefits of adopting low pressure casting can lead to significant savings. The process reduces waste and minimizes the need for extensive finishing work, thus cutting down on production costs. This makes it an attractive option for small businesses striving to optimize their budgets.
3. Increased Production Efficiency
With faster cycle times compared to traditional casting methods, the low pressure casting process allows businesses to increase their output. This efficiency enables companies to meet growing demand, particularly in the competitive fields of product design and 3D printing.
4. Versatility in Design
One of the most significant advantages of the low pressure casting process is its versatility in handling various designs and materials. From artistic sculptures to complex mechanical parts, this process can adapt to a wide range of applications. For businesses in art supplies, this opens up a world of possibilities for innovative product offerings.
Applications of Low Pressure Casting in Different Industries
The implications of the low pressure casting process extend far beyond metal casting. Let’s explore its application across different industries, focusing on how businesses can integrate this technique into their operations.
Art Supplies
In the art supplies industry, low pressure casting is frequently used to create custom tools, molds, and artistic pieces. Artists can utilize metal casts that are both lightweight yet strong, allowing for dynamic creations that retain structural integrity. Furthermore, the ability to reproduce detailed textures and patterns enables artists to bring their visions to life with precision.
Product Design
For businesses in product design, the low pressure casting process provides a framework to create prototypes that are not only functional but also aesthetically pleasing. Designers can experiment with metal finishes and textures, leading to the creation of innovative products that stand out in the market. Moreover, the quick turnaround time allows designers to rapidly iterate on their concepts and get products to market faster.
3D Printing
The intersection of low pressure casting and 3D printing is particularly fascinating. By creating highly detailed molds using 3D printing technology, manufacturers can utilize the low pressure casting process to produce complex metal parts that would be nearly impossible to achieve through other means. This synergy can drive innovation and efficiency, making it a valuable strategy for businesses looking to push the envelope of design and manufacturing.
Choosing the Right Partner for Low Pressure Casting
To fully capitalize on the benefits of the low pressure casting process, businesses must choose the right partner. Here are key factors to consider when selecting a casting service:
- Experience: Look for companies with a proven track record in low pressure casting. Their expertise can significantly impact the quality of the final product.
- Technology: Ensure that the partner utilizes advanced equipment and techniques to produce high-quality casts. State-of-the-art technology translates to better precision and faster delivery.
- Material Options: A diverse range of material choices allows for greater flexibility in design. A good partner should offer various alloys to meet your specific needs.
- Customer Support: Strong communication and support are critical. Choose a partner that is responsive and willing to collaborate closely throughout the project.
The Future of Low Pressure Casting in Business
As industries evolve, the low pressure casting process is likely to play an increasingly pivotal role in shaping the future of manufacturing. With the push towards sustainability and eco-friendliness, innovations in low pressure casting may lead to the development of new materials and methods that reduce environmental impact.
Embracing Sustainability
The future of the low pressure casting process will not only revolve around efficiency and quality but also sustainability. Manufacturers are increasingly looking for ways to minimize waste and energy consumption, integrating recycled materials into their processes wherever possible. This shift will appeal to a conscious consumer base and set businesses apart in a crowded marketplace.
Integration with Advanced Technologies
The integration of smart technologies and automation in low pressure casting processes will further enhance efficiency and reduce human error. The use of IoT devices to monitor and streamline operations can significantly improve production outcomes, allowing businesses to respond swiftly to market demands.
Conclusion
The low pressure casting process is redefining how businesses approach manufacturing in various fields, particularly in the realms of art supplies, product design, and 3D printing. By embracing this innovative technique, businesses can enhance product quality, reduce costs, and increase efficiency. As we head into the future, those who leverage the advantages of low pressure casting will undoubtedly find themselves at the forefront of their respective industries.
For businesses looking to elevate their offerings and gain a competitive edge, understanding and implementing the low pressure casting process is not just an option—it's a necessity. By investing in the right partnerships and technologies, you can not only meet customer expectations but exceed them, setting a foundation for long-term success in a dynamic marketplace.